Introduction: Friction Folding Knife (Higonokami)
In this era of computers, internet, and... I don't know, airplanes!? a pocket knife is an underrated tool. You need something to open all those Amazon packages, don't ya? (Ironically, pocket knives are not too airplane friendly.) If you're a "maker," like me, then having a versatile tool with you also means that making something new is never too far away.
There's plenty of knife tutorials on Instructables, some of them quite good, but I couldn't find any that felt like a solid introduction to knife making (a practice I recently began and love) as well as a guide to making a genuinely useful knife.
So here we are.
Remember- take it slow, measure twice, and it will never be perfect the first time, so don't be afraid to try again.
Safety First
Always wear eye protection. Ventilate smoke. Stay aware of hot metal.
Step 1: Tools, Materials, Set Up
What you'll need:
Materials:
- Small washers (optional)
- "Hardenable" tool steel (high carbon steel, maybe 4"x1")
- A rivet pin (we'll get to this, but essentially a small, straight cylinder of metal)
- Choice of handle (I used brass, a piece twice the width of the blade plus the thickness of the metal x the length of the blade portion + a little bit- for my knife this was maybe 2 1/2"x 3")
Tools:
- Bench grinder (or equivalent, files would work, for instance, but I won't go into that here)
- Drill press
- Band saw
- Hammers (ball peen is ideal- basically a hammer with a sphere on the end)
- Anvil/hard and stable striking surface
- Layout tools- even a sharpie and ruler will do, calipers really help
- Sandpaper, Scotch-Brite, wire wheel- cleanup tools
- Strong heat source- I use an acetylene torch
- Oil- some people use vegetable oil! I used Parks Quench Oil- 70 I think
- Table vice
That's it! If it sounds like a lot, don't worry- almost all the large or expensive tools can be substituted for an angle grinder, drill gun, palm sander, or other affordable tools.
Step 2: Mistakes, Planning, and Extra Material
I hope you like the bright yellow work paper!
A great place to start is with drawings. Unfortunately, I didn't make any- so here are some after-the-fact! (Refer to the pdf- I don't recommend it as a template, but it will give you a sense or placement and proportion.)
I started by cutting a knife shape and the handle form on the band saw. The initial knife shape was pretty straightforward- "blade" with a long tail that will work well as a handle and lever, and "handle" with holes to serve as a pivot point, and a slot for the tail piece.
The center rectangle should be about the width of the thickness of your knife metal, plus a little extra for washers. The placement of the holes was tricky- I found a good spot by cutting out my knife piece and kind of imagining how it would pivot. You want the blade to be completely covered by the brass when "sheathed" (rotated in) and you want as much blade as possible when rotated out.
Consider printing and cutting out the pdf drawings, putting a pin through the holes, and seeing how it all fits together- you can make your own custom template this way, too.
We all make mistakes.
Zoom in on the brass. See how both sides of the handle have double dimples? I couldn't decide where to put the hole, so I marked the spot twice. At least I didn't drill it. I thought it would be cool to have a spiral tail. It broke, after an hour of work. It sucked, but I kept going and made something I'm proud of.
Attachments
Step 3: Annealing, Texturing, and Drilling
Once you have your handle marked out and the small slot is cut, it's time to give it some flair- this is entirely optional, but that texture just feels sooooo good. I did this by using a ball peen hammer to make dimples in the surface of the brass that would face out. Once the brass gets too hard, don't try to force it- heat it until it turns a dull red, then throw it in water (quench it). This is called annealing, and it's a process by which metal is relaxed to become more workable.
Either before or after texturing, drill holes for the hinge in the handle. The important thing is that they are symmetrical to each other across the center line of the handle. To drill a perfectly sized hole, measure the piece of rod you're using with calipers or a micrometer, and use a drill bit with the same diameter. If you don't have a ton of drill bits, that's fine! Go for the next closest size up.
Once your handle is satisfactory, fold it! There are a number of ways to do this- I clamped mine and bent it around a ninety degree corner, then again around a piece of metal with a thickness that I liked. Take it slow- if it gets wonky (it did for me) and the holes become misaligned, anneal it, and work it a little more. Hole alignment and having the slot in the middle of the handle are the most important bits.
EDIT
When you have the drill press set up to drill your handle, go ahead and drill your pivot point in your blade blank too. (That's the unsharpened but roughly cut material that'll become your knife.) You can put a nail or something similar through you handle and blade to check that the blade rotates to the position you want it to.
Step 4: The Grind
Grinding a blade can be daunting. Once you have your blade cut out, and a hole drilled where you want it, approach the grinder (with confidence- you are gonna own this grind). Practice on some metal first, to get a sense of angle and control.
I like to hold a work piece in some Vice Grips- you don't have to, but if you don't, dunk it frequently so it stays cool and holdable. I encourage you to research bevel types, but if you're lazy like me, here's a crash course.
The bevel is the "blade" part of a blade, where it goes from the thickest part (the spine) the the thinnest (the edge). There's loads of types of bevels, which we won't get into. A great, functional, and simple bevel is the flat bevel- a flat transition from the spine to the edge.
To grind, hold your work piece at an angle against the grinder. The angle your hold your work piece at will be mirrored by the grind- I like to grind nice and long, almost as if I'm just pressing the flat of the blade against the grind, but at the slightest angle. Make sure the edge doesn't look wonky- you want it to taper to the tip but still be sharp along the whole length.
Grinding is an art, to be learned by doing. If you want this knife to be perfect, practice on scrap metal a lot. This is my fifth or sixth knife, so I'm just starting to feel good about my grinds. Find photos of knives you like and try to emulate those.
I start with a 60 or 80 grit sandpaper, and move up to 120, then, 320 or 400 off the grinder. A wire wheel or scotch-brite pad makes a knife surface really shine.
Keep it simple stupid
I decided to grind just one side of my knife this way. It gave me some problems down the line, but a single-sided grind is fast and simple, since the sides don't need to be close to symmetrical.
(NOT MY BEVEL EXAMPLE IMAGE)
Step 5: Handle Refinement
Around this point I was going back and forth from working on the handle to working on the blade. I did some test fits, placing washers around the blade and then sliding it into the handle, with my rivet pin holding the whole thing together. I rotated the blade this way, and realized I had a whole ton of extra handle! I marked what I could lose and ground it down until I had a smooth and organic shape. With my blade and handle done, it was ready for heat treatment.
Step 6: Heat Treatment
Heat treatment describes the process of hardening steel (making it crystalline) and then gently relaxing it, to make it strong and springy. Start by setting up a quiet area with your heat source, vice, pliers (or gloves, a rag could work- something to grab a hot knife with) scotch-brite, and quenching oil. Make sure you can heat the knife without setting anything on fire.
First we harden. Apply heat to the blade until it all turns an even, cherry red- I like to start at the spine, so by the time it's hot enough the thinner blade will be ready, too. As soon as you evenly achieve this color, quickly dunk the whole knife in oil. Stir it around, watching out for flames. After a couple stirs, take it out and make sure it's straight. Small bends can be gently corrected. Use the table vice to grip the blade, and very slowly reverse any kinks- check your work frequently, since you only have about ten seconds. If there are still bends after that window closes, thats okay! Reheat the blade to cherry red and then let it air cool. After that you can straighten it and try again.
After hardening, you can cool the blade in water or oil. Clean off the oil with scotch-brite to produce a shiny surface, so you can see the small color change in the temper.
I slightly over-tempered my edge- it heats up faster than the spine- but the middle of the blade is perfect. You're going to want to aim for that same "wheat gold" color. To achieve it, slowly apply heat to the blade, and very gently. Try to get the whole blade that same pale or dark gold, then quickly place it in oil to lock that chemical state in place. Your steel should now be springy, robust, and able to be sharpened.
Step 7: Assembly!
The blade assembly is simple. Put all the pieces together, and cut down the rivet pin, leaving about 1/2 the diameter of the rivet sticking out on either side. Against an anvil and with a ball peen, strike the rivet, spreading it out to securely hold everything in place. Do this on either side, and that's it! Your blade will be quite hard to rotate from the start- break it in by opening and closing it.
Enjoy your new pocket knife! I hope this was as fun to follow as it was to write, and make sure to let me know how it goes!
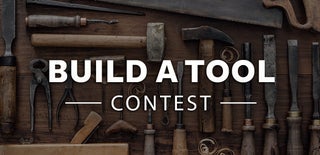
Participated in the
Build a Tool Contest